The BioRobotics Laboratory at the Cleveland Clinic has created and launched a new robotics testing technology for orthopaedic biomechanics research that integrates with ATI Multi-Axis Force/Torque Sensors. This system known as simVITRO provides new insight into how the body is designed, how orthopaedic implants will perform, and the potential outcomes of surgical interventions. The simVITRO system combines software, hardware, and integration services to create a universal musculoskeletal simulator that can provide in vitro simulation of major joints including the spine, knee, foot/ankle, hip, shoulder, elbow, wrist, and more.
Real time force feedback control is at the core of simVITRO’s control technologies. The ATI line of Multi-Axis Force/Torque Sensors is well matched for the needs of the simVITRO system. simVITRO is hardware neutral and works with a large variety of robots to test a wide array of joints requiring a broad range of loads. The breadth of the ATI product line, from the Nano all the way up to the Omega, provides a common solution for force and torque control whether it is the lower loads required to articulate the smaller joints in the hand or higher loads required for knee or foot testing.
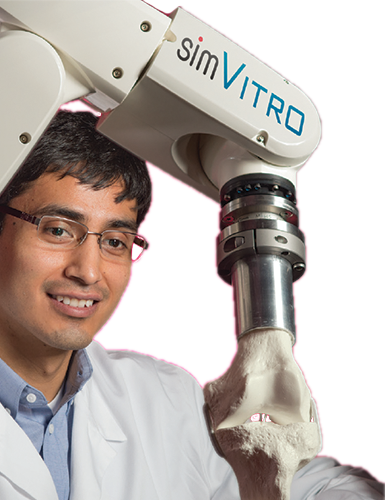
Since 2003, the BioRobotics lab has been using ATI Force/Torque Sensors for all of their in-house robotic musculoskeletal testing systems, and with the launch of simVITRO as a product, ATI F/T Sensors have been shown to be an ideal choice for the next generation of these systems. Robb Colbrunn, Director of the BioRobotics Lab at the Cleveland Clinic stated, “The benefit we get from working with ATI is not simply the force/torque sensors themselves, but also the signal conditioning hardware and engineering product support that all work together to provide a turnkey solution for simVITRO.”
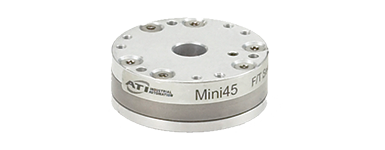
The ATI Multi-Axis Force/Torque Sensor system measures all six components of force and torque. The system consists of a transducer, shielded high-flex cable, and intelligent data acquisition system, Ethernet/DeviceNet interface or F/T controller. Force/Torque sensors are used throughout industry for product testing, robotic assembly, grinding, and polishing. In research, ATI F/T Sensors are used in robotic surgery, haptics, rehabilitation, neurology, and many others applications.
More information on ATI Force/Torque Sensors here.
More information on simVITRO here.